Community
1 November, 2024
World first in Warrnambool
A WORLD first engineered wood product made exclusively from locally grown bluegum (Eucalyptus Globulus) timber has been manufactured in Warrnambool.
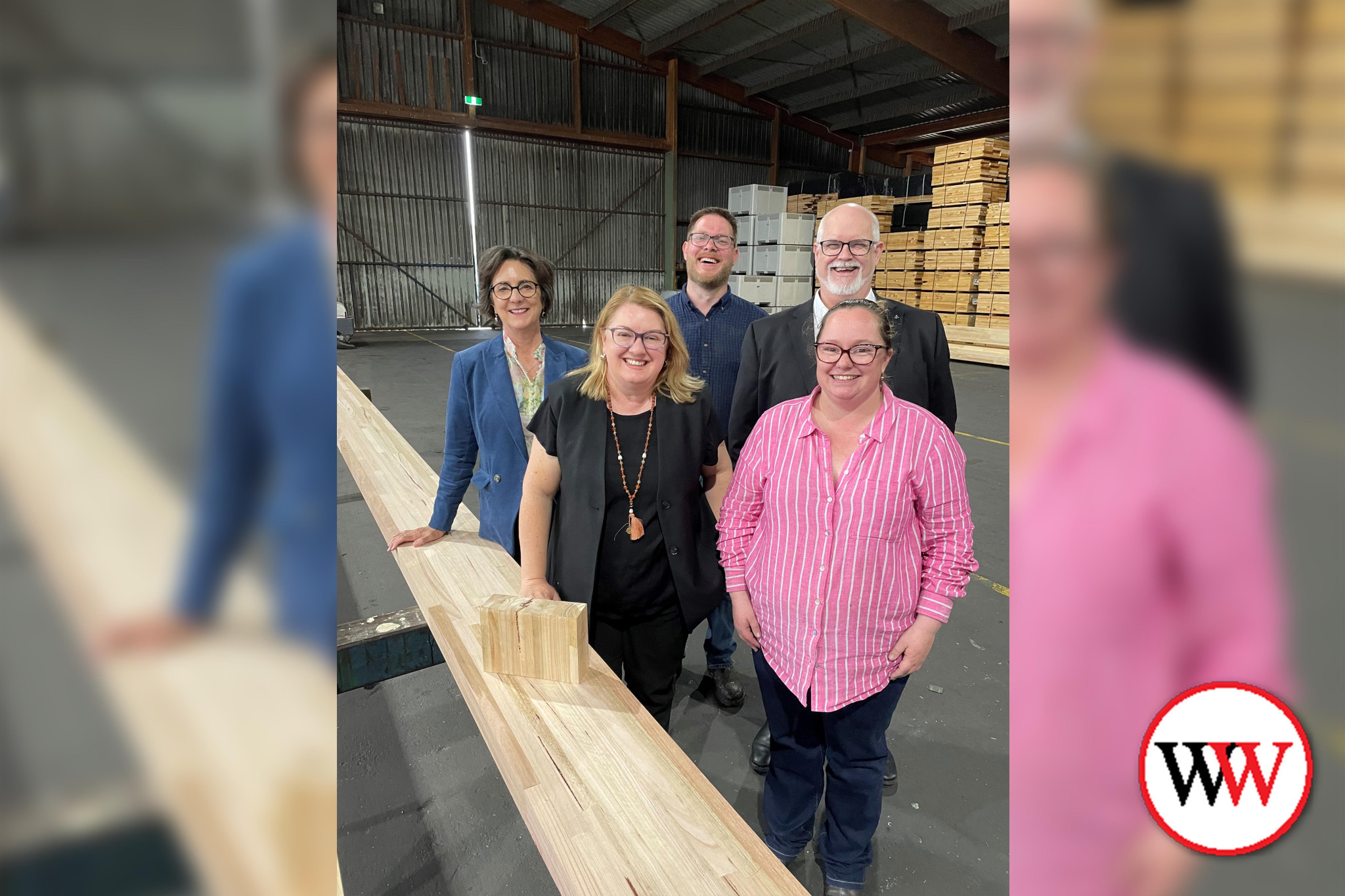
This new product provides a pathway to address Australia’s growing structural timber market demand.
The Green Triangle Forest Industries Hub and Forest and Wood Products Australia, working in partnership with WTIBeam (formerly known as Warrnambool Timber Industries), have unveiled the first of its kind GL18 timber product.
This product can be utilised in everything from flooring to roof framing in both residential and commercial construction.
It is envisaged that the laminated glulam product, produced from glued and finger jointed laminates, will help fill the void from the state’s cessation of native forest harvesting while reducing the state’s reliance on imports from volatile offshore markets.
Victoria is Australia’s biggest importer of structural timber, sourcing more than 40 per cent of its market base, with demand anticipated to quadruple by 2050 due to population growth and urbanisation.
The Splinters to Structures project, funded by the federal government, focused on creating new domestic value from the plantation hardwood trees that are traditionally exported to Asian markets including China and Japan.
Victorian Minister for Jobs and Industry Natalie Hutchins and Member for Western Victoria Jacinta Ermacora met with the research group earlier this week.
Discussions centred around how the product could fit into conventional and modular constructions to fill the state’s housing market demand.
Minister Hutchins said this was an exciting product with wide potential.
“This new, world-first wood product has the potential to address timber demand and help our booming construction industry who are working around the clock to build more homes across Victoria,” Minister Hutchins said.
Green Triangle Forest Industries Hub chief executive Tony Wright said the research group planned to use the findings to undertake commercial trials, building a pathway to commercialisation.
“These commercial trials will help us understand how we best replace native hardwood with plantation hardwoods with a product that already has a broad domestic base,” Mr Wright said.
“Ultimately, its envisaged that this bluegum GL18 product could be utilised in both domestic and commercial builds and is perfect for use in a prefabricated building, acting as a replacement for concrete or steel.
“The outcome for the sector is reduced reliance on exports, the creation of new local jobs and a cost-effective building material with a positive carbon outcome that can fix a shortfall in the domestic market.”
WTIBeam owner Edwina Vulcz, whose father Tim Goodall is a key figure in glulam product development and founder of the business, said their team had been “pleasantly surprised” by the trial outcome.
“Historically trials had only looked at structural framing, which failed in a commercial setting because of challenges in sawing,” Ms Vulcz said.
“This is a completely different scenario. Bluegum (Eucalyptus Globulus) lends itself to glue laminated timber production because of its suitability in a more hands on manufacturing application.
“This product has the potential to save thousands of dollars in the construction of a home because you have a smaller beam that can be utilised further because of its strength, reducing the need for other materials.”
GTFIH deputy chair and board director of Australian Bluegum Plantations (ABP) Laurie Hein said the low carbon product was paving the way for a more diversified regional market base.
This, he believed, would address the imbalance between supply and demand.
“The Hub has always been focused on optimising the use of every piece of fibre grown in our region and we see this latest development as an important milestone,” Mr Hein said.
“While we work towards strengthening the intelligence from our existing trials, the next major step is to undertake a feasibility study.
“This will allow us to understand how to take this product to scale through the construction of a manufacturing hub, developing multi-generational jobs and capturing as much economic value in the supply chain as possible.”
The Splinters to Structures project is supported by Green Triangle-based hardwood plantation companies including Australian Bluegum Plantations, Midway Limited, New Forests (SFM Management and PF Olsen).